Ensuring optimal truck performance isn't complicated. It's all about regular maintenance checks, spotting issues before they escalate, monitoring fleet condition, and adopting preventive methods. Scheduled maintenance and service guarantee optimal uptime, better productivity, and protection. Expert guidance from experienced technicians can help you master fleet maintenance through the smart implementation of digital tools, detailed record-keeping, and skilled staff. Start exploring this comprehensive guide to fleet maintenance and unlock economical operations. There's much to explore and master!
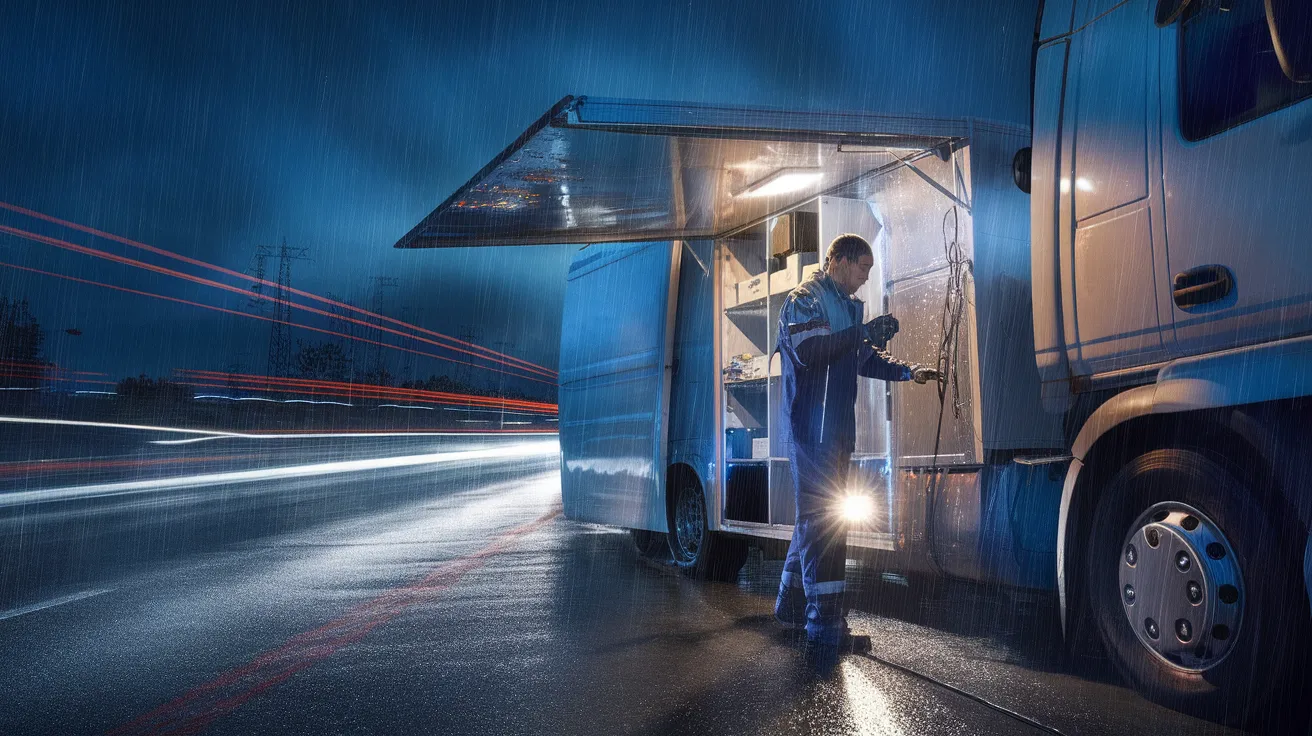
Critical Findings
Recognizing the Critical Role of Regular Truck and Fleet Upkeep
Though it could feel overwhelming, getting a handle on regular truck and fleet maintenance is crucial for any thriving operation. You'll find the advantages of maintenance far outweigh the time and effort invested. Regular checks and servicing can significantly extend your vehicles' longevity, avoiding hefty replacement costs. Furthermore, there's an undeniable connection between regularly maintained fleet and improved fuel efficiency. This translates to decreased fuel spending, boosting your overall cost efficiency. Additionally, routine servicing can help identify small problems before they escalate into major ones, preventing costly repairs later on. Therefore, never discount the power of scheduled servicing; it can be a real game-changer for your company's profitability.
Examining Key Components of a Successful Maintenance Framework
To guarantee your fleet's longevity and efficiency, it's crucial to recognize the fundamental aspects of a well-designed maintenance program. You'll have to grasp the basic principles of maintenance, monitor the health of your fleet regularly, and implement preventive measures in advance. With these in place, you're well on your way to decreasing downtime and optimizing productivity.
Key Maintenance System Features
When it comes to improve your fleet's efficiency and lifespan, establishing a robust maintenance program is essential. Key components of the program consist of scheduled inspections, systematic servicing, and proactive repairs. Each aspect plays a crucial role in minimizing costly breakdowns and reducing downtime. While the benefits of a maintenance program are substantial, you must consider the implementation challenges. These may include operational difficulties and team reluctance. Yet, with careful preparation, effective messaging, and commitment to education, these challenges can be overcome. Remember that an successful maintenance program goes beyond fixing problems; it averts them. It's an dedication in your fleet's future – and it's one that will yield significant returns.
Fleet Condition Monitoring
As you delve into the fundamentals of a effective maintenance program, understanding the critical role of fleet condition monitoring takes center stage. It extends beyond ensuring vehicle functionality, it focuses on enhancing fleet performance. Monitoring technologies offer a comprehensive view of your fleet's health, empowering you to identify potential issues before they become serious.
Such tracking solutions track key metrics like fuel consumption, tire pressure, engine check here status, and more. Through analyzing this data, you're not just guaranteeing the longevity of your fleet but also minimizing unnecessary repair costs. Remember timely discovery is key in fleet management. Thus, invest in dependable monitoring solutions and stay ahead of the curve. Don't merely address problems, anticipate them. Maintain your fleet's optimal condition and your operation will operate efficiently.
Implementing Preventive Measures
Although tracking your fleet's condition is crucial, establishing preventive protocols is equally critical to secure a effective maintenance program. It's important to identify potential problems before they escalate into expensive repairs and operational delays. So, let's talk preventive measures.
An important approach is establishing a comprehensive maintenance checklist. This document should outline all required inspections, maintenance procedures, and component updates. Regular engine checks, tire rotations, and oil changes are a given. Make sure to include smaller components like windshield wipers, lights, and filter components.
Make sure your checklist contains a schedule for each task. Sticking to this timeline makes certain that your fleet remains in peak condition. Remember, proactive maintenance reduces costs, time, and troubles in the long run.
Critical Regular Inspections for Truck and Fleet Maintenance
To make certain your fleet and trucks remain in optimal condition, you must prioritize regular maintenance inspections. These checks include regular service evaluations and essential system reviews. By adhering to these essential protocols, you'll extend your fleet's durability, optimize operational performance, and consequently, minimize costly repairs.
Scheduled Service Checks
Regular maintenance inspections represent your primary safeguard from unplanned vehicle and fleet malfunctions. These inspections offer you the ability to detect and fix problems before they turn into costly repairs or dangerous accidents. One of the primary benefits of routine maintenance is the avoidance of service interruptions, which can substantially influence your company's productivity and bottom line.
Key Component Evaluations
Following up on the importance of scheduled maintenance inspections, let's examine the specific essential component checks that must be carried out regularly to ensure peak truck and fleet performance. Start with the brake system – verify all components are operating correctly, from brake pads to fluid levels, as well as checking for leaks. When overlooked, brakes might fail, leading to catastrophic incidents. Checking tire pressure is equally essential. Underinflation increases fuel consumption and tire wear, while overinflation can cause a blowout. Obtain a quality pressure gauge for accurate readings. Keep in mind tires should be cold during checks for optimal results. Routinely carrying out these essential checks can help avoid costly repairs and potential accidents. Drive safely on the road.
Strategic Maintenance Planning for Fleet Optimization
While overseeing a fleet, it's vital that you emphasize preventative maintenance to guarantee peak efficiency. Establishing a comprehensive preventative scheduling system is crucial. This minimizes unnecessary wear and tear, and lowers the probability of unscheduled downtime. You should schedule regular inspections and maintenance based on engine hours, mileage, time, or fuel usage. Note that each vehicle is unique and might need a customized approach.
Maintenance education serves as another vital strategy to secure peak efficiency. Provide your staff with the necessary skills to spot potential issues before they escalate. This reduces downtime but also minimizes expenses. The combination of scheduled prevention and maintenance education will create a highly effective and reliable fleet. Prevention is always better than cure.
Expert Recommendations for Commercial Vehicle Service and Rehabilitation
Even though fleet and truck maintenance and restoration might appear challenging, understanding the process can make it much simpler. The first thing you should do should be to learn about different maintenance methods. This knowledge will allow you to spot concerns swiftly and accurately. Following this, arrange maintenance work based on the extent of repairs needed and the truck's function in your operation. Frequently check all units for potential issues and address them promptly to prevent further damage. Keep in mind, restoration isn't just about fixing issues, it's aimed at upgrading the truck's performance and lifespan. Lastly, make sure to select top-grade materials for restoration; they'll provide better durability and performance. Remember these guidelines, and you'll navigate fleet maintenance and renovation with ease.
Harnessing Technological Advances for Advanced Fleet Management
To maintain a competitive edge in the trucking industry, it's crucial to harness industry innovations for advanced fleet maintenance. Innovation in the field are rapidly changing the maintenance landscape. Embrace data analytics to analyze your fleet's operations and predict potential issues in advance.
State-of-the-art monitoring systems can track and monitor engine health and efficiency, fuel consumption, and driver behavior patterns. Utilize this crucial data to implement preventive maintenance, helping reduce costly operational interruptions.
Never ignore software updates. These improvements generally contain essential fixes and improvements that boost your vehicles' safety and performance. Be aware that fleet management extends past mechanical care. You're working in a technology-driven era, and staying current with sector developments will support your fleet's durability and financial performance. By utilizing effective processes, you can minimize costs and time, and safeguard human life.
Common Questions
What Skills Should a Professional Vehicle Fleet Mechanic?
You'll need a valid certification, fulfilling the standards of an accredited mechanic institution. Moreover, you require a thorough skill assessment, showing your expertise in multiple facets of fleet service and repair. Professional experience is also important!
What's the Recommended Tire Replacement Schedule for Fleet Vehicles?
Similar to clockwork with the changing seasons, you need to examine your fleet's tire wear regularly. Nevertheless, it's typically best to install new tires every three to six years, based on usage and road conditions.
What Are the Common Signs of Engine Trouble in Trucks?
You can detect engine issues in trucks from signs such as abnormal engine noises and poor fuel performance. Additional indicators are heavy smoke emissions, fluid leakage, or a check engine light that won't turn off.
Does Technology Play a Role in Improving Truck and Fleet Maintenance?
Technology plays a vital role in improving truck maintenance. Telemetry systems deliver real-time data, while smart systems anticipate issues before they happen. You'll observe minimized maintenance delays, enhanced security and as a result, cost savings. It's a game-changer.
Do Different Fleet Vehicles Have Unique Maintenance Requirements?
Different vehicle types certainly require specific maintenance schedules. One must account for the vehicle's purpose, weight limits, and operating terrain, as these elements greatly influence needed upkeep. Always adjust maintenance based on the type of vehicle.
Summary
In the end, the key is maintaining optimal fleet performance, wouldn't you agree? Regular maintenance isn't just a suggestion, it's absolutely necessary. By identifying key components, performing regular inspections, implementing proactive measures, and leveraging technological advances, you're doing more than basic maintenance, you're developing a high-performance fleet. And keep in mind, vehicle maintenance isn't a setback, it's a pathway to enhancement. Stay committed, and you'll experience your fleet's productivity, consistency, and lifespan achieve new levels.